Plastic extrusion specialists delivering exactness and quality
A Comprehensive Guide to the Process and Advantages of Plastic Extrusion
In the large world of manufacturing, plastic extrusion emerges as a extremely effective and essential process. Translating raw plastic into continual accounts, it caters to a huge selection of sectors with its exceptional versatility.
Comprehending the Essentials of Plastic Extrusion
While it may show up complicated in the beginning glance, the procedure of plastic extrusion is basically simple - plastic extrusion. It is a high-volume manufacturing method in which raw plastic is thawed and shaped into a continual account. The procedure begins with the feeding of plastic material, in the kind of granules, powders, or pellets, right into a warmed barrel. The plastic is then thawed utilizing a mix of warmth and shear, applied by a turning screw. Once the molten plastic gets to completion of the barrel, it is compelled via a little opening known as a die, forming it into a desired type. The shaped plastic is after that cooled, strengthened, and reduced right into wanted lengths, finishing the procedure.
The Technical Refine of Plastic Extrusion Explained

Sorts Of Plastic Suitable for Extrusion
The selection of the best kind of plastic is a crucial facet of the extrusion procedure. Various plastics offer one-of-a-kind buildings, making them much more fit to specific applications. Polyethylene, for instance, is commonly used because of its low expense and simple formability. It uses exceptional resistance to chemicals and dampness, making it ideal for products like tubing and containers. In a similar way, polypropylene is another popular choice due to its high melting factor and resistance to tiredness. For more durable applications, polystyrene and PVC (polyvinyl chloride) are usually picked for their stamina and durability. These are usual alternatives, the selection ultimately depends on the certain demands of the product being generated. Comprehending these plastic types can dramatically boost the extrusion process.
Comparing Plastic Extrusion to Various Other Plastic Forming Methods
Recognizing the sorts of plastic suitable for extrusion leads the means for a more comprehensive discussion on just how plastic extrusion compares to other plastic creating methods. These consist of injection molding, strike molding, and thermoforming. Each approach has its unique uses and benefits. Shot molding, for example, is outstanding for developing elaborate components, while strike molding is excellent for hollow items like containers. Thermoforming excels at forming superficial or huge parts. Nonetheless, plastic extrusion is unparalleled when it pertains to creating constant accounts, such as seals, gaskets, and pipelines. It likewise permits a consistent cross-section along the length of the item. Thus, the option of technique greatly relies on the end-product demands and specs.
Trick Advantages of Plastic Extrusion in Manufacturing
In the realm of manufacturing, plastic extrusion supplies many considerable benefits. One noteworthy benefit is the cost-effectiveness of the procedure, that makes it an economically attractive manufacturing approach. Furthermore, this method supplies superior item adaptability and boosted manufacturing rate, consequently boosting total manufacturing performance.
Affordable Manufacturing Method
Plastic extrusion jumps to the leading edge as an economical manufacturing approach in production. In addition, plastic extrusion calls for less power than conventional manufacturing approaches, adding to lower functional costs. In general, the monetary benefits make plastic extrusion a very eye-catching option in the manufacturing industry.
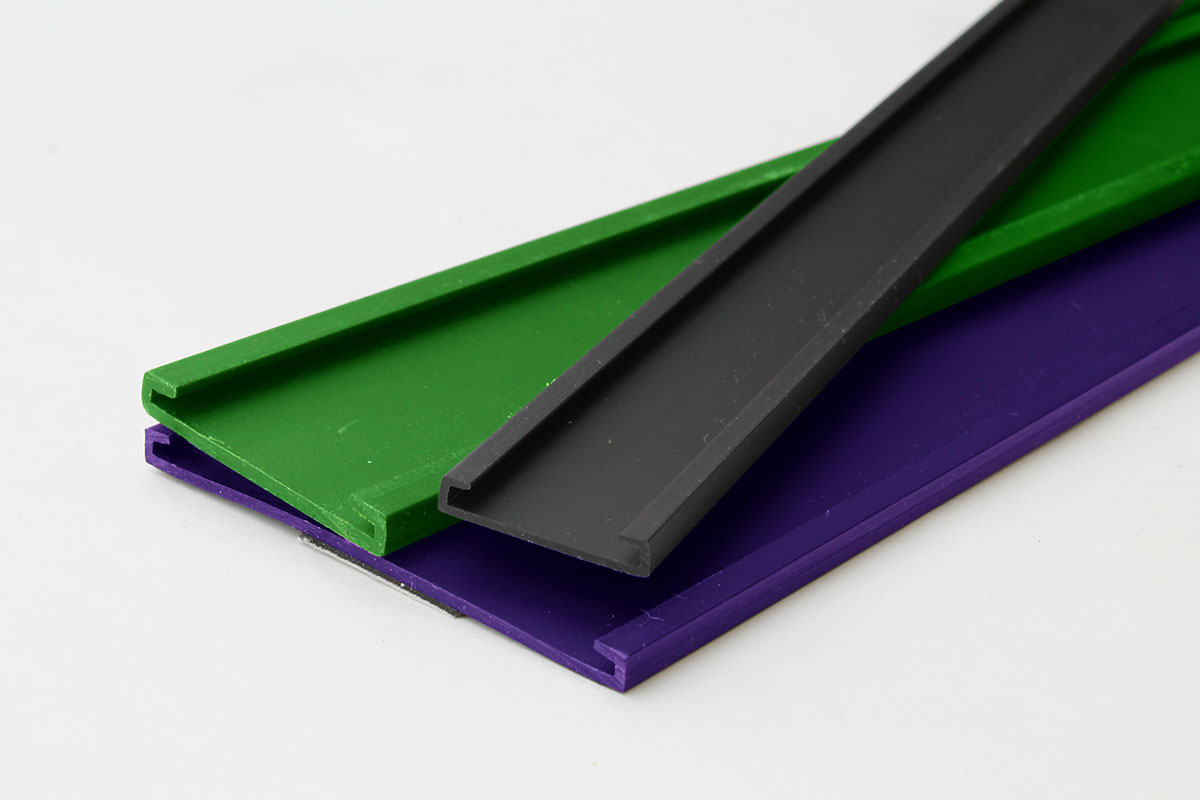
Superior Product Flexibility
Past the cost-effectiveness of plastic extrusion, an additional considerable benefit in manufacturing lies in its premium item versatility. This makes plastic extrusion a perfect remedy for sectors that need tailored plastic components, such as automobile, building, and packaging. In essence, plastic extrusion's product versatility promotes innovation while improving functional performance.
Improved Production Speed
A considerable advantage of plastic extrusion lies in its boosted production speed. This manufacturing process enables for high-volume manufacturing in a relatively short time span. It is capable of creating long, constant plastic accounts, which significantly minimizes the manufacturing time. This high-speed production is especially beneficial in sectors where large quantities of plastic components are needed within tight deadlines. Few other manufacturing processes can match the speed of plastic extrusion. Furthermore, the capability to maintain constant high-speed production without compromising product high quality establishes plastic extrusion here in addition to various other techniques. The boosted manufacturing rate, consequently, not just makes it possible for producers to satisfy high-demand orders however likewise adds to boosted performance and cost-effectiveness. This helpful function of plastic extrusion has actually made it a recommended option in various industries.
Real-world Applications and Effects of Plastic Extrusion
In the world of production, the technique of plastic extrusion holds profound value. This process is extensively made use of in the manufacturing of a plastic extrusion range of items, such as plastic tubing, home window frameworks, and weather removing. Because of this, it greatly affects industries like building and construction, product packaging, and vehicle industries. Moreover, its effect includes day-to-day products, from plastic bags to tooth brushes and disposable cutlery. The economic advantage of plastic extrusion, largely its cost-efficient and high-volume outcome, has transformed production. Nevertheless, the environmental influence of plastic waste remains a worry. The sector is constantly striving for advancements in recyclable and biodegradable products, showing a future where the advantages of plastic extrusion can be maintained without endangering ecological sustainability.
Conclusion
To conclude, plastic extrusion is a extremely effective and efficient method of changing raw products into varied products. It provides numerous advantages over other plastic forming approaches, consisting of cost-effectiveness, high outcome, minimal waste, and layout versatility. Its effect is profoundly felt in various sectors such as building and construction, vehicle, and consumer items, making it a crucial webpage process in today's manufacturing landscape.
Digging much deeper into the technological procedure of plastic extrusion, it starts with the choice of the suitable plastic product. As soon as cooled down, the plastic is cut into the called for lengths or wound onto reels if the product is a plastic film or sheet - plastic extrusion. Contrasting Plastic Extrusion to Various Other Plastic Forming Methods
Recognizing the types of plastic suitable for extrusion leads the method for a broader conversation on how plastic extrusion piles up versus various other plastic forming approaches. Few various other production processes can match the rate of plastic extrusion.